传感器的应用对实现整体工业系统的优化作用时很重要的,是当今我们在使用机械设施和技术系统时面临的一些核心挑战。这个话题不仅在工业领域,在任何使用机械系统的地方都变得越来越重要。
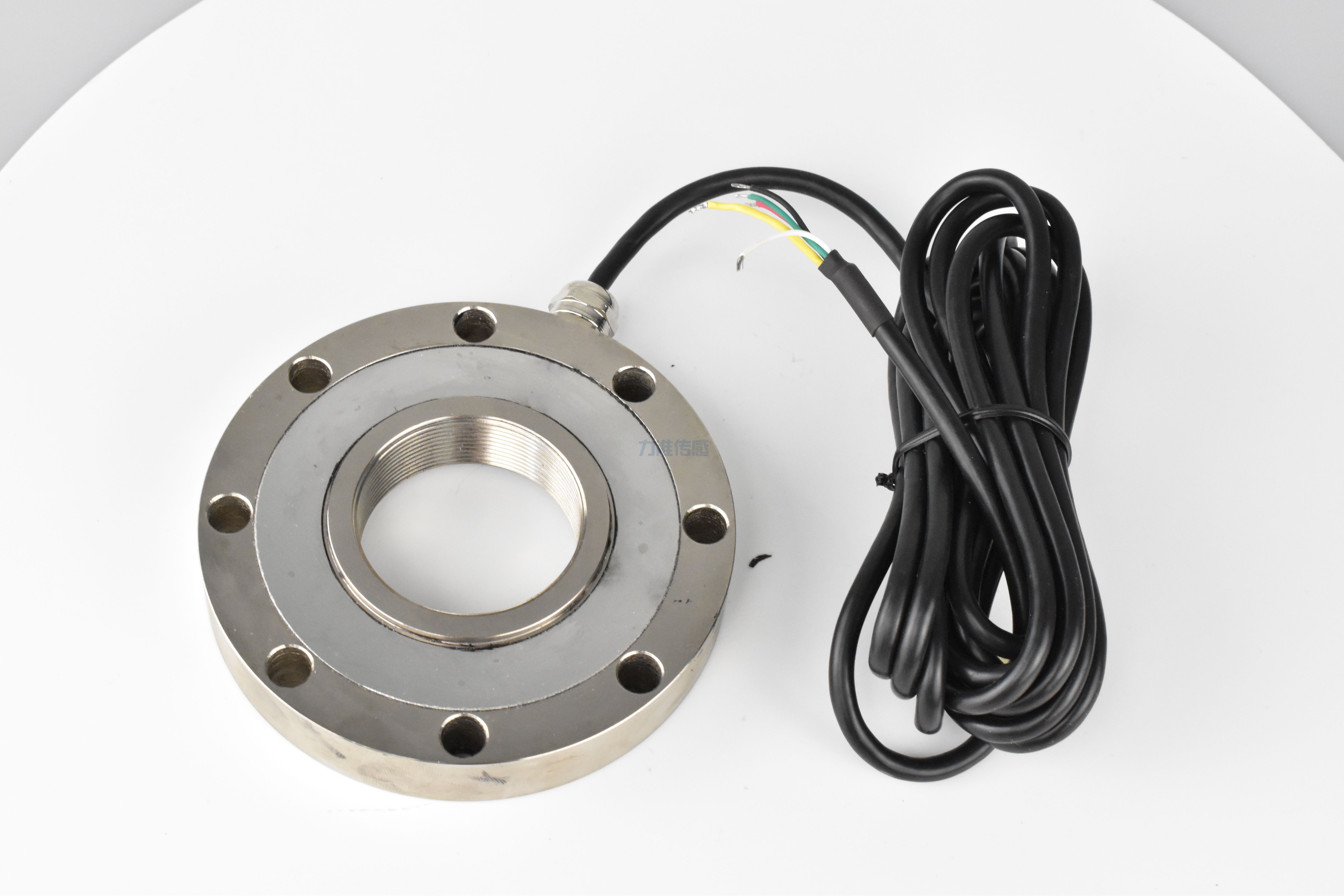
在过去,机器按计划维护,延迟维护可能面临生产和停机的风险,如今,人们通过处理机器数据来预测剩余的使用寿命。特别是对于温度、噪声、振动等关键参数,记录的数据可以用来确定最佳运行状态甚至所需的维护次数,这样可以避免不必要的磨损,尽快发现潜在的问题和原因。通过这种状态监测,可以挖掘出相当大的优化空间,从而获得决定性的优势。比如ABB1一年内停机时间减少70%,电机服务寿命延长30%,设施能耗减少10%。
预防性的维护一个重要组成部分是基于状态监测(CBM),通常监测涡轮机、风扇、泵、电机和其他旋转机。然而,传感器的本身并不会提供故障或磨损预测,这些只能通过预防性维护和检测。
在状态监测方面,可能需要考虑以下基本问题:
一般从逻辑上讲,从发现问题到开始维护的间隔越短越好,然而,熟悉机器特性的专业人员需要依靠知识和经验来判断,以优化运行和维护成本,或充分发挥设施的最高效率,这些专业人员主要来自轴承/润滑领域,在电机分析方面经验不多,属于最薄弱的环节。
未来对传感器维护服务的需求是什么?这属于生命周期的早期阶段,不排除故障,但概率相对较小,一般与生产故障有关,只有在下一个定期维护阶段,接受相应培训的维护人员才会开始进行有针对性的干预。
继续讲一下,机械的输出速度、齿轮比和轴承部件的数量与机器的振动模式分析密切相关。一般来说,齿轮箱引起的振动反映在频域的轴速倍数上,而轴承的特征频率通常不代表谐波重量。此外,湍流和气蚀引起的振动通常被检测到,它们通常与风扇和泵中的气流和/或液流有关,因此通常被视为随机振动。
在机械维护包养的过程中,机械内部的多轴传感器也可以用来记录各个方向的振动,但根据其物理特性,单轴传感器噪音更低,测量范围更广,带宽更大,所以更加需要注意保养。